TECHNO TUBE
We are the production plant with modern equipment for the manufacture welded round and profile stainless steel tubes.
Capacities of the enterprise allow to produce up to 1000 tons of pipes per month. The products are certified by ISO and TUV.
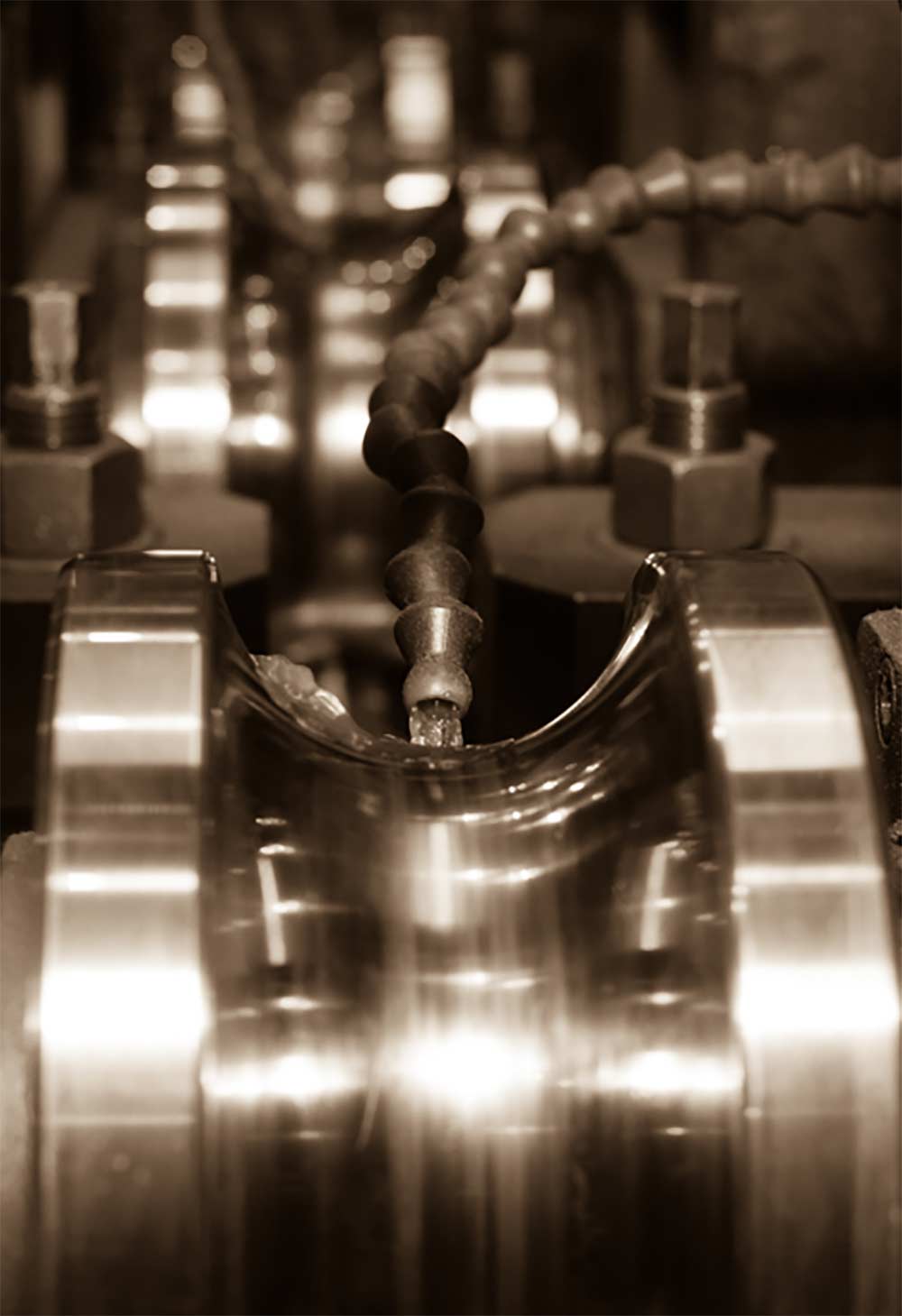
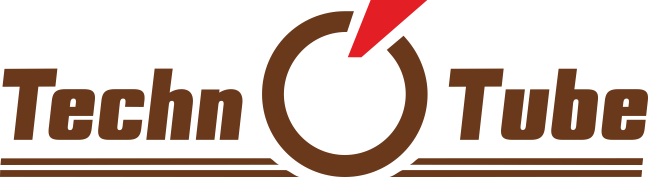
PRODUCTION CAPACITY
- 6 TIG welding mills and 3 laser mills.
- Polishing workshop.
- Longitudinal slitting machine for the coils with the thickness from 0.8 mm to 6 mm.
- Machinery for equipment’s repair, modernization and its consumables production.
- The annual tubes output is 20 000 tonnes.
For the tube production we used only high quality raw material (EN 10088-2) from world famous producers.
All our products undergo strict quality control:
- Tensile test
- Flattening test
- Test of the distribution
- Leakage test
- Dimensional control
- Visual examination of the surface
- Non-destructive test (eddy current)
- Pneumatic control (hydraulic test)
HISTORY OF THE PLANT
2009
Investment project, decision regarding company's establishment was done, purchase of land and equipment.2010
Dommercial operation of the enterprise with 3 TIG mills has been strated.2011
Start of constructional pipes production.2012
Production capacity were expended up to 5 TIG mills. The trial production of tubes for application in food and pharmaceutical industries.2013
Production of tubes for the sugar industry and the heat exchanger tubes of austenitic and ferritic steels. Bright annealing furnaces were purchased.2014
Certificate of quality management system ISO 9001: 2008 has been recieved. Laboratory was built. Start running of 2 Italian mills.2015
Laser mill with production speed of up to 30 meters per minute has been implemented. Trial production of ASTM A249 standard tubes.2016
Production capacity is up to 4500 tonnes per year. Expansion of the production range. Capabilities for profile tubes polishing has been implemented.2017
2 Olimpia`s laser lines have been purchased. Capabilities for profile tubes polishing has been implemented.2018
Ability to produce big diameter tubes (up to 114 mm).The new tube polishing manufactory and warehouse have been built. The line for the grinding and mirror polishing of profile tubes in sizes of from 10x10 to 100x100 mm has been launched. The new line for the mirror polishing of round pipes in the range of diameters from 12 to 52 mm has been installed. A co-generating gas plant has been settled for production autonomy.